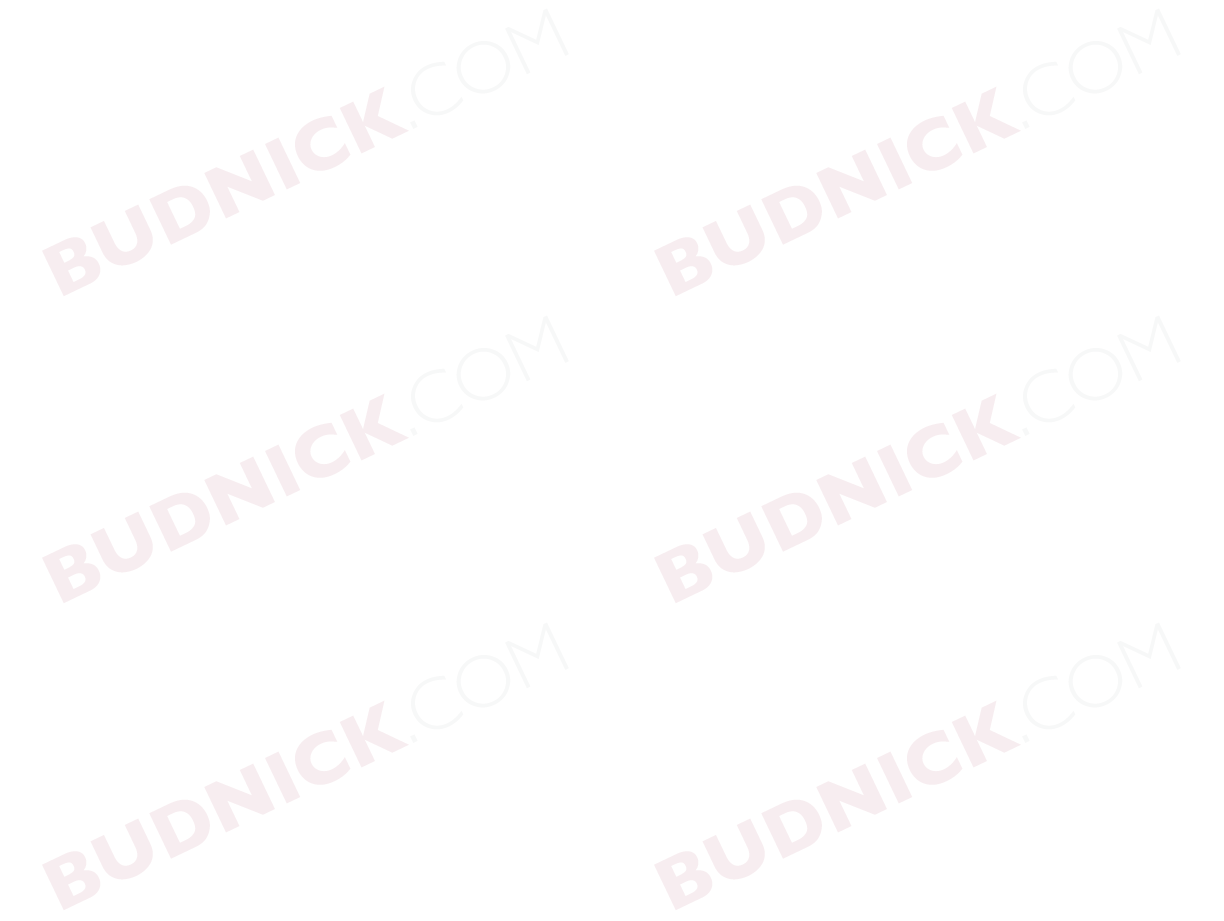
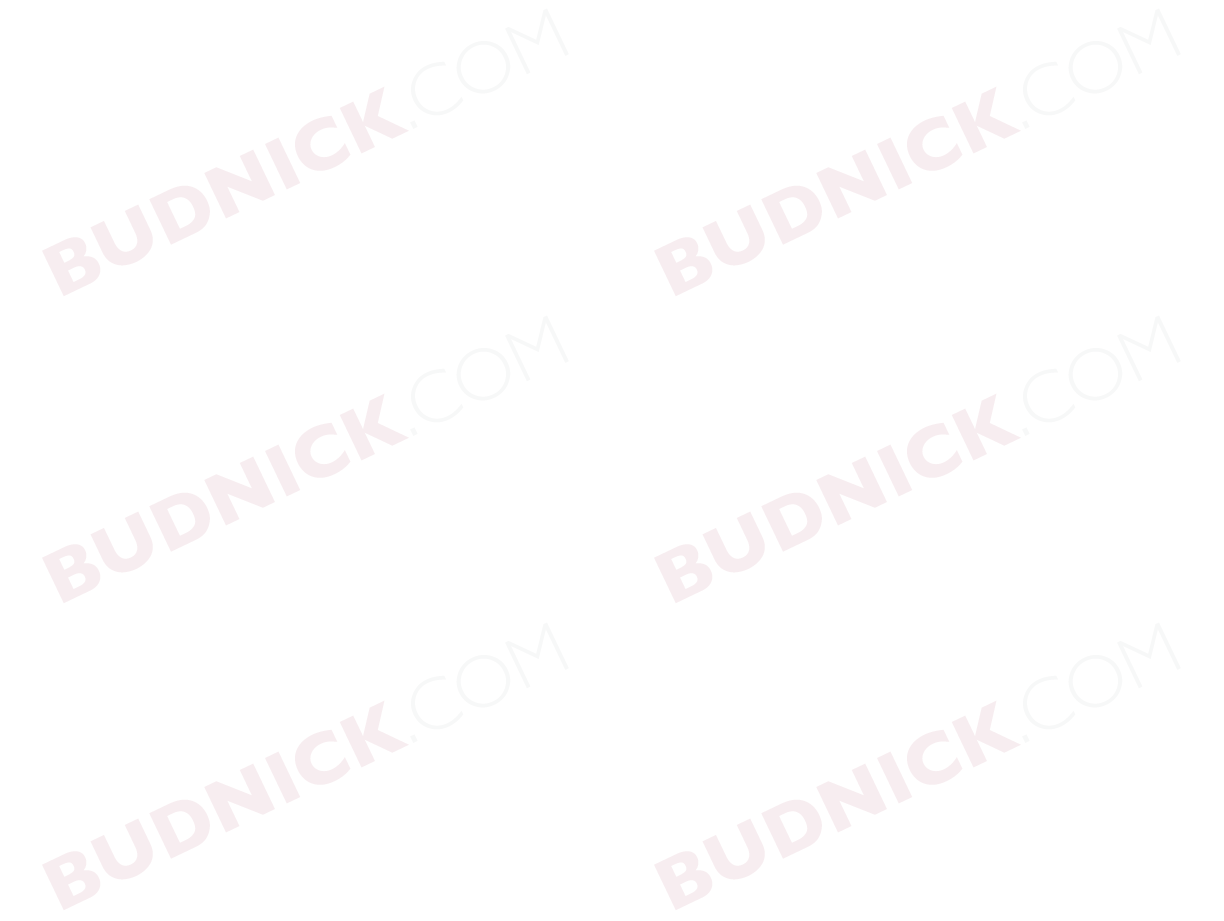
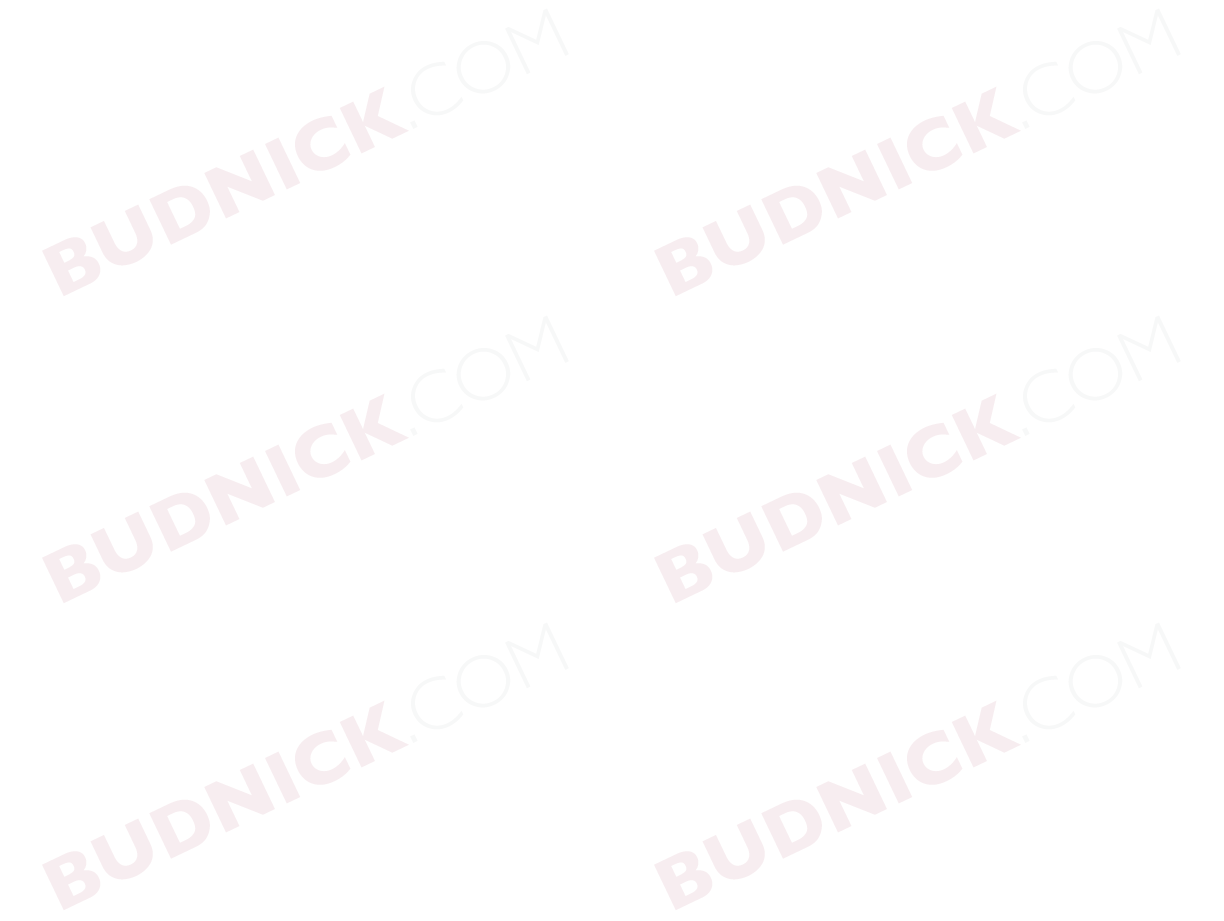
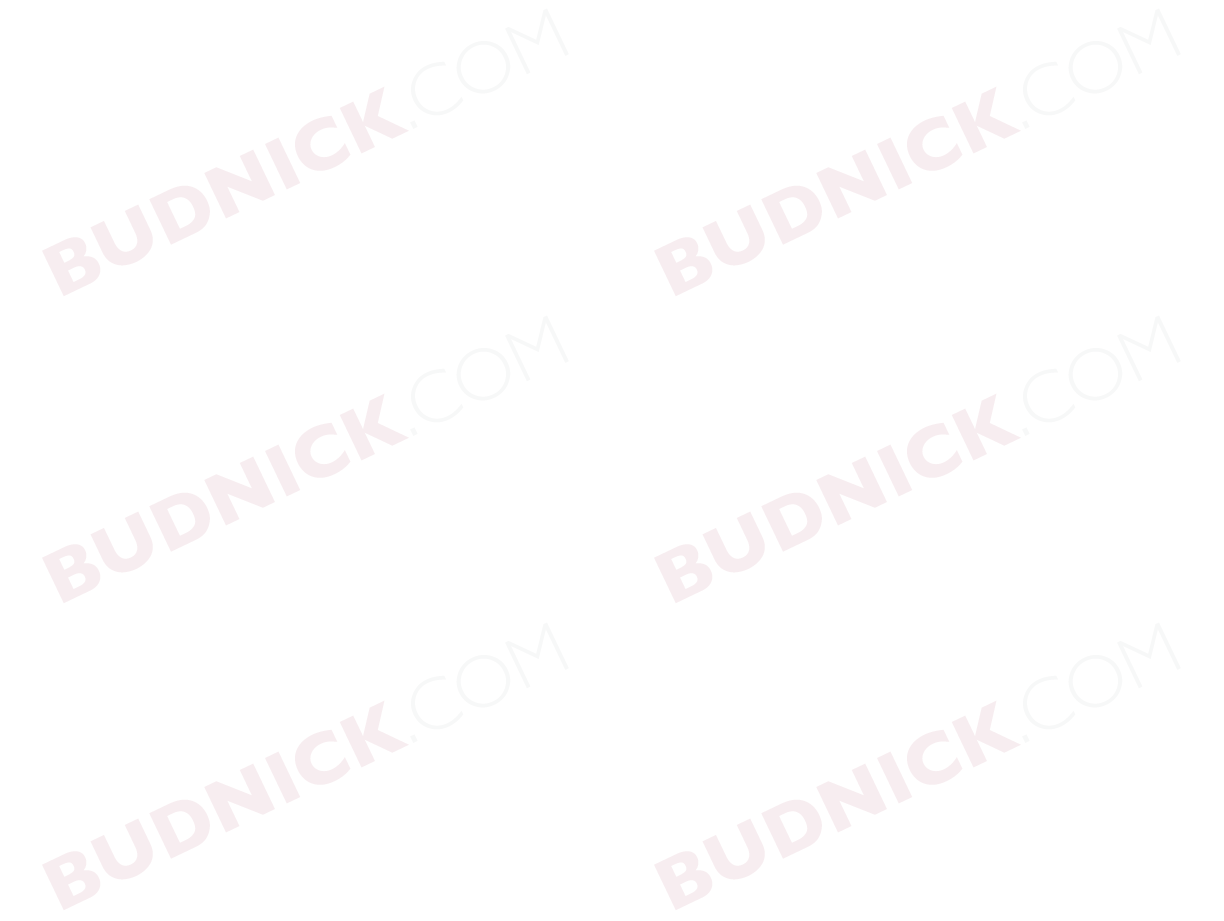
Manufacturing Engineer
Budnick Converting, Inc., headquartered in Columbia, IL (in the St. Louis, MO metropolitan area), is a privately held and female owned corporation. Budnick’s primary focus is specialty converting of adhesive coated tapes and foams. Budnick remains on the leading edge of adhesive tape converting technology; currently utilizing over 70 die-cutting, slitting, laminating, printing (including flexographic printing), label making and spooling machines to convert materials into labor saving customized parts. For more information on Budnick, please visit our website at www.budnick.com.
POSITION PURPOSE: Responsible for designing, implementing, and reviewing the procedures involved in the manufacturing processes. Focus on cost reduction opportunities in the facility. Liaison between the estimation, production, and quality departments to promote an efficient and well-organized manufacturing operation.
ESSENTIAL FUNCTIONS:
- Review engineering part design drawings and tool layouts prior to production release to ensure most cost effective and efficient design.
- Review high dollar parts for most efficient production methods and material yields.
- Analyze existing systems and processes and identify value-added and non-value-added activities to solve design challenges. Evaluate manufacturing processes based on scrap loss, process efficiency and speed.
- Assists in the monitoring of daily production activities and makes recommendations on process changes to promote efficiency of operations. Identify opportunities for preventing waste and inefficiencies during production.
- Manage cost reduction program for the facility. Research, calculate, implement, and track all suggestions submitted by employees.
- Support production by improving struggle or operator high stress parts.
- Design and develop robust manufacturing concepts to simplify and improve processes, ensuring that designs are producible and within manufacturing capabilities.
- Prepared product and process reports by collecting, analyzing, and summarizing information & trends. Create and maintain required documentation for manufacturing processes, including flow charts, capacity and utilization studies, time and motion studies, standard work, cycle time analysis and line balancing.
- Design, develop and test new and existing production procedures; automated and non-automated to meet company efficiencies and objectives.
- Improve manufacturing efficiencies by analyzing facility layout and planning workflow, space requirements and equipment layout.
- Work with BOM Specialist with questions regarding the set-up Bill of Materials in the ERP System.
- Collaborate with Estimators to calculate & provide accurate cost estimates and define production methods to finalize request for estimates in a timely manner.
- Assists in making recommendations on in-house vs outside vendor manufacturing capabilities. Assists in evaluating the requirements for assembly tooling, fixtures and equipment purchases needed to support the manufacturing operations.
- Perform duties safely and maintain an elevated level of safety awareness. Ensure that manufacturing procedures follow safety and environmental regulations.
OTHER RESPONSIBILITIES:
- Assist in the development of long-term estimating strategies & help implement the plan(s) developed. Communicate ideas and accomplishments to the Estimation Manager.
- Assist in the training of new department employees.
- Alert Estimation Manager to conditions that create delays or affect quality of production work in a timely manner, assisting in adjustments and changes needed to meet established deadlines.
- Participate in R&D projects to further the companies’ capabilities.
- Follow operation standards and all department policies and company directives and assist with other projects and tasks as required by management.
- Conduct any special manufacturing projects, evaluation or surveys as directed by management.
- Travel to customers, suppliers, and trade shows to support the company and increase fabricating knowledge. Could be 10 to 20% travel.
KEY QUALIFICATIONS:
Knowledge: Clear understanding of the converting business; manufacturing processes, fabrication methods and tool design. Working knowledge of estimation processes. Product knowledge and capabilities.
Skills: Strong analytical and problem-solving skills. Strong mechanical aptitude. Takes initiative. Should have a working competency with all office equipment. Good interpersonal, written and communication skills required.
Ability: Conduct business in a professional, positive, and courteous manner. Listen effectively, respond clearly, write legibly, and read a variety of written orders/instructions. Work cooperatively with a variety of individuals. Gain the confidence and trust of others. Adapt to interruptions, changes, emergencies, repetition, and pressure without losing effectiveness and composure. Quickly grasp new concepts, approaches, or systems. Employ resourcefulness when problem solving to meet customer needs.
Education: High School diploma or equivalent required. Bachelor’s degree in industrial, manufacturing, or mechanical engineering preferred. CAD experience required (2D minimum). Basic Lean Sigma concepts, methodologies, and tools helpful. Working knowledge of Microsoft Office products required.
Experience: Converting knowledge with adhesive tape and foam or previous experience at a manufacturing company a plus.
Quantitative Data: Must be able to remain in stationary sitting position for prolonged periods of time. Must be able to frequently move about the office and production facilities to access file cabinets, machinery, etc., constantly operate a computer and other office productivity machinery, such as copy machine and computer printer. Physical ability to do work requiring frequent stooping and bending. Sufficient vision acuity (corrected) to read instructions, view production machine set up, and visually inspect parts produced. This position requires frequent communication with other employees; must be able to exchange accurate information in these situations.
Hours: 8:00am – 4:30pm, M-F, In-person position.
FLSA Class: Exempt
Reports To: VP of Operations
Pay: $70,000 - $80,000 / year
BENEFITS: We offer a full-benefit package including the following, that are paid 100% by the company: vacation, holidays, $25,000 of life insurance and short-term and long-term disability benefits. We also offer medical (premium cost shared with the company), dental & vision insurance and a 401K retirement plan with a company match of 25% of the 1st 6% the employee contributes.
Interested Candidates should apply on-line at www.budnick.com, under About Us - Careers.
Equal Opportunity Employer
THE ABOVE STATEMENTS ARE INTENDED TO DESCRIBE THE GENERAL NATURE AND LEVEL OF WORK PERFORMED BY PEOPLE ASSIGNED TO THIS CLASSIFICATION. THEY ARE NOT TO BE CONSTRUED AS AN EXHAUSTIVE LIST OF ALL JOB DUTIES PERFORMED BY THE PERSONNEL SO CLASSIFIED.
Location:
340 Parkway Drive
Columbia, IL 62236
Hours:
M-F 8am - 4:30pm CST