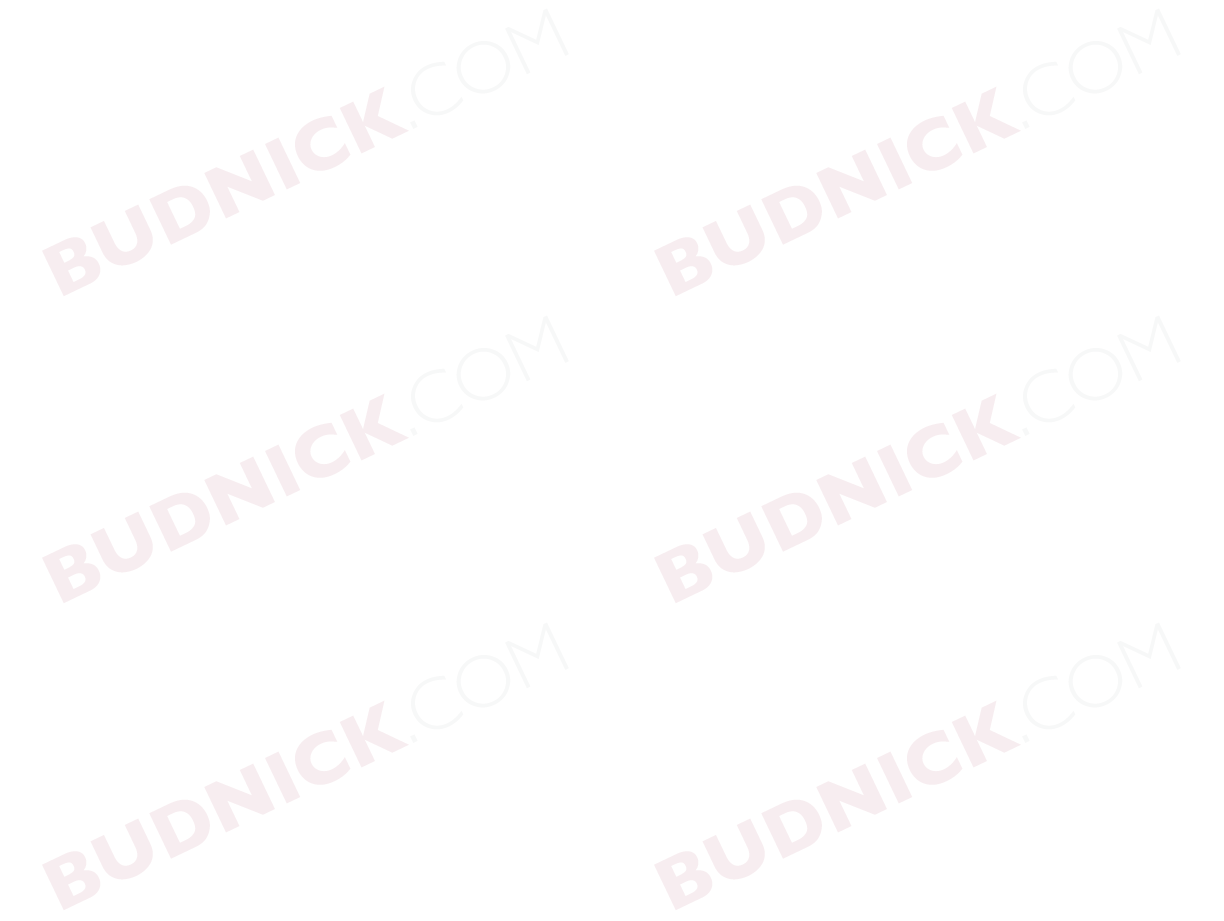
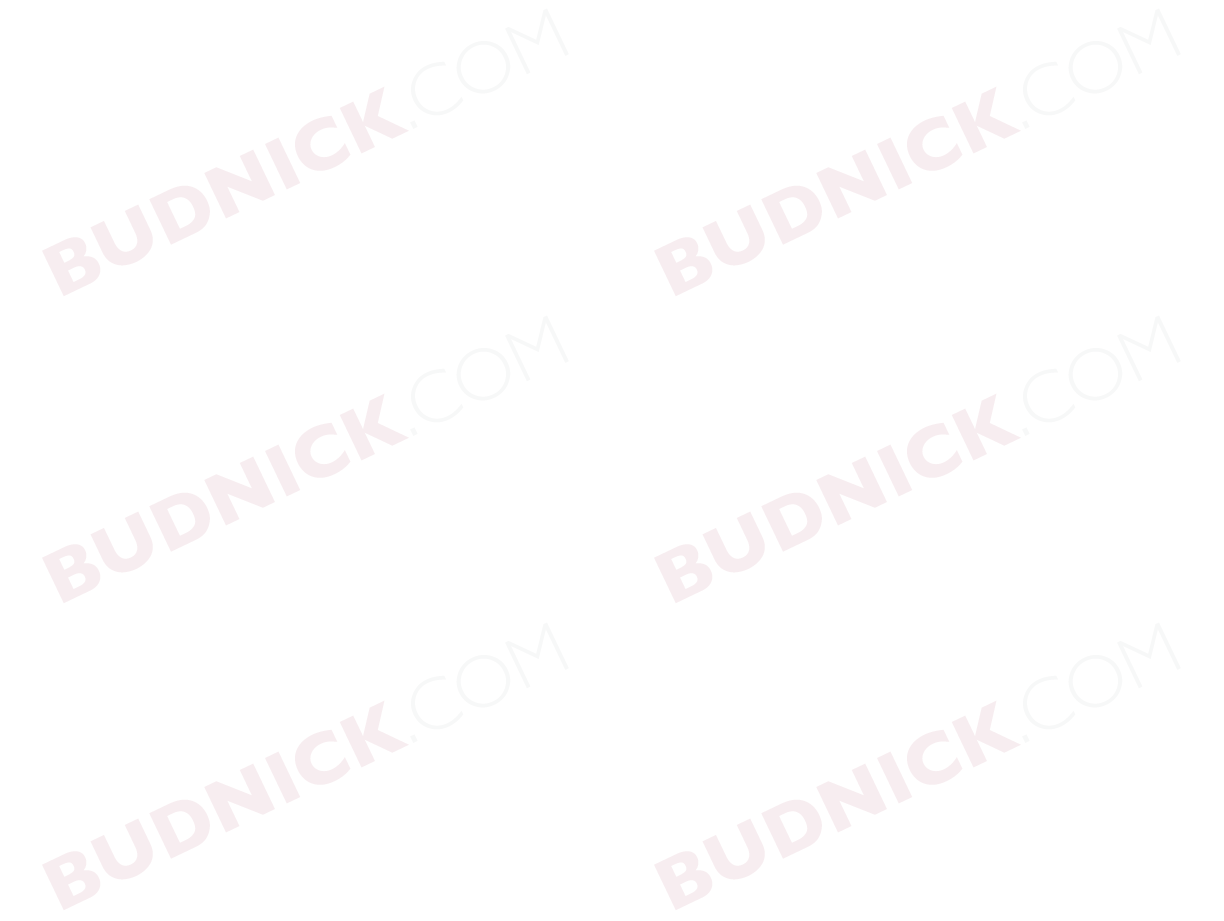
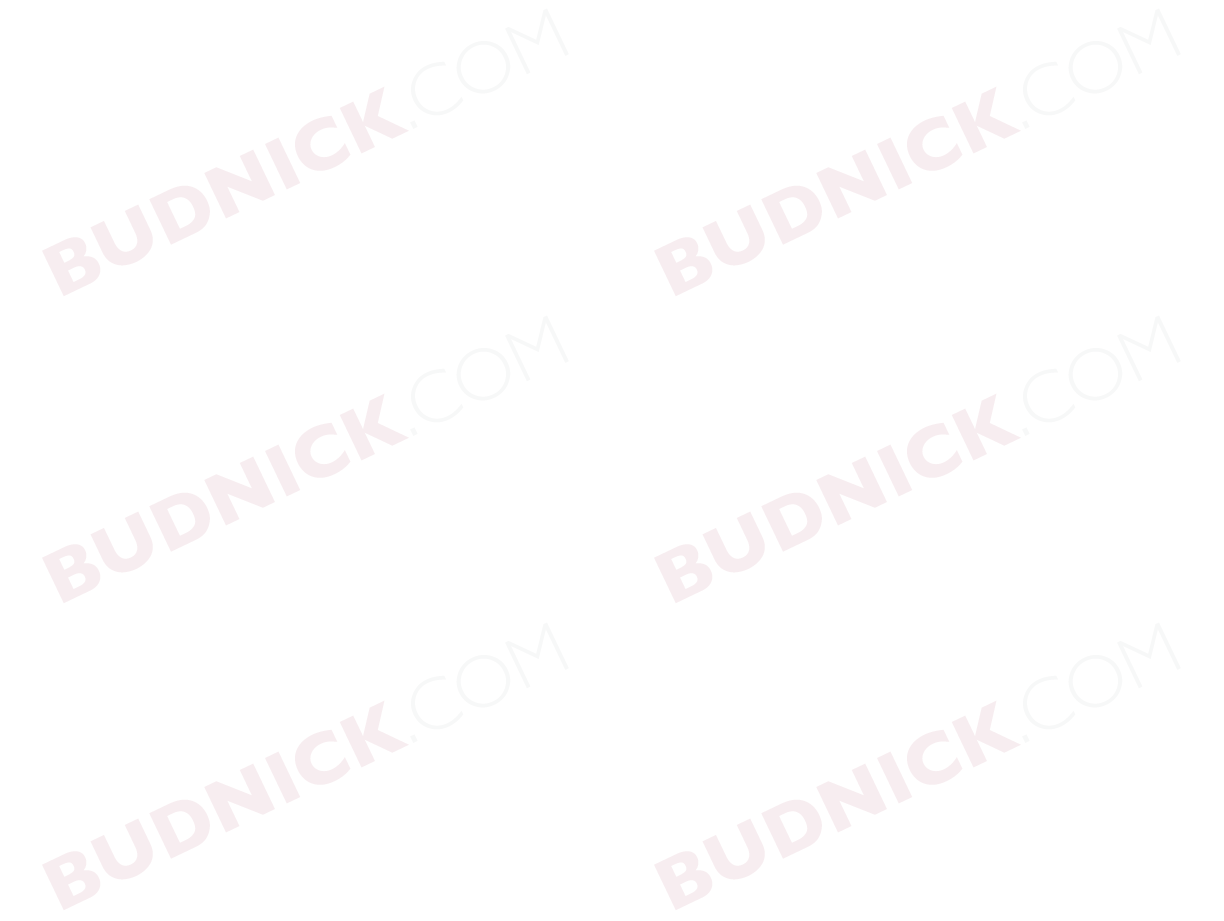
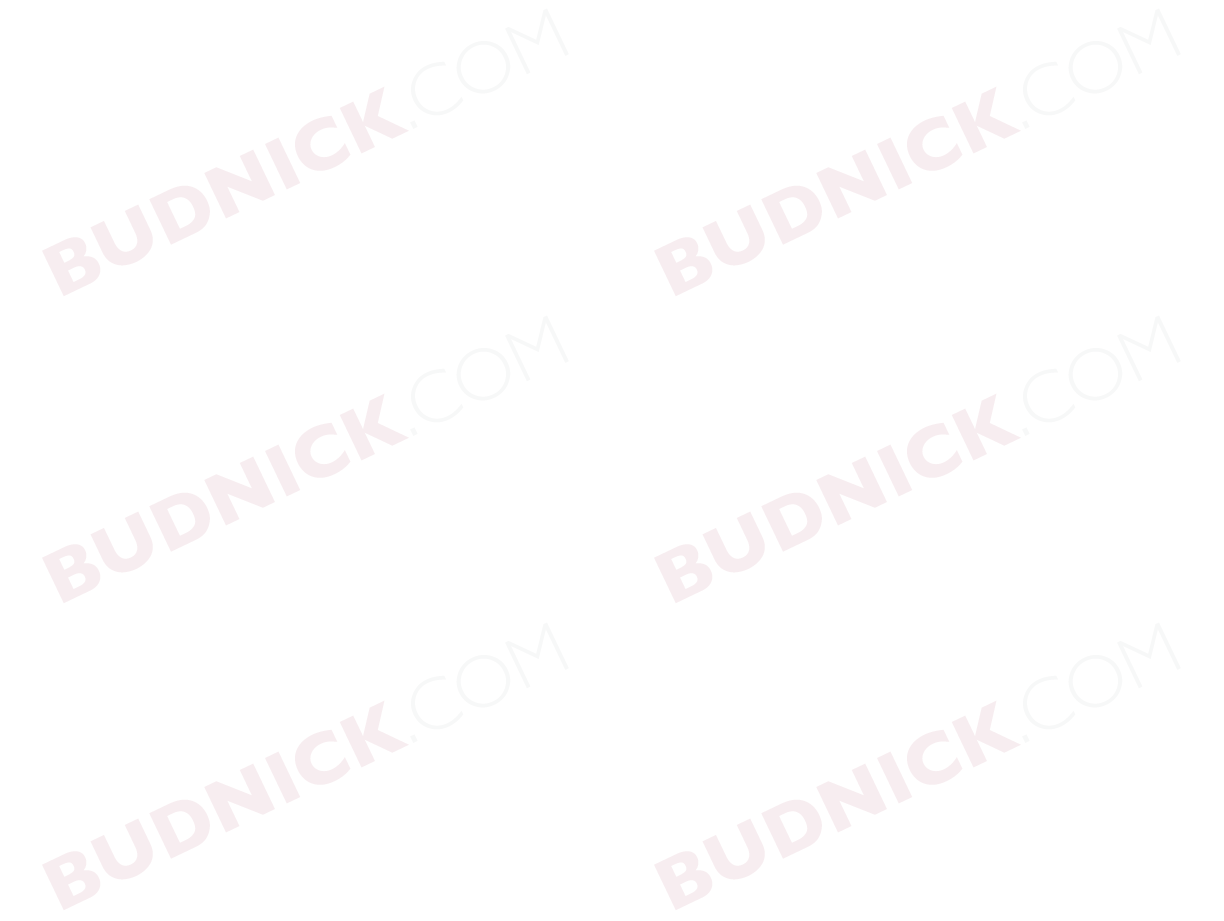
Tape101
One of the biggest missteps you can make in your adhesive selection process is assuming that all tapes are the same - which is why we're here to help you understand the differences.
Get the eBook
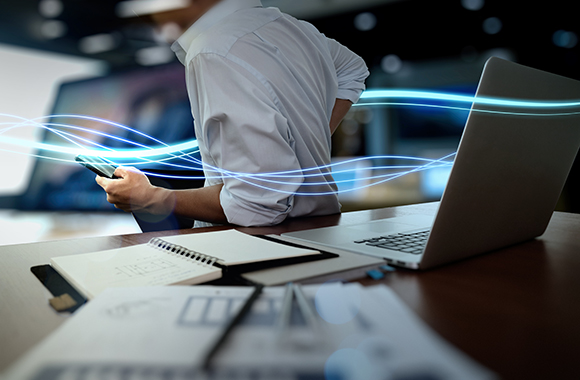
One of the biggest missteps you can make in your adhesive selection process is assuming that all tapes are the same. So much goes into whether an adhesive will work for your specific application, and you should consider each factor when picking out an ideal product. It's important to match the properties of your adhesive to the needs of what you're bonding.
At Budnick.com we've always made it our primary goal to educate our customers as best we can, and our Tape101 eBook and learning center is the next step in that process. We've outlined the basic steps to follow and questions to ask throughout the process of identifying an adhesive so you can approach each project with the knowledge you need to make the best decisions. Feel free to browse through the basics of tapes, or for a more in-depth overview, download our free eBook here!
Case Studies
Budnick has decades of experience developing application, product, and process solutions - read about some of our favorite solutions below!
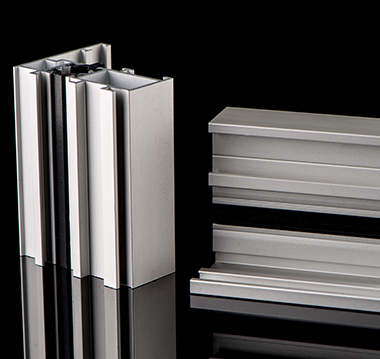
Case Study Efficiency
Working in tandem with our distribution customer, we were able to identify an ideal solution for the end user, improving both production efficiency and the bottom line.
- Distributor approached Budnick regarding their customer, a vinyl window manufacturer
- By modifying the final format we were able to reduce machine stoppage dramatically
- Several options were presented to consider and implement in their processes
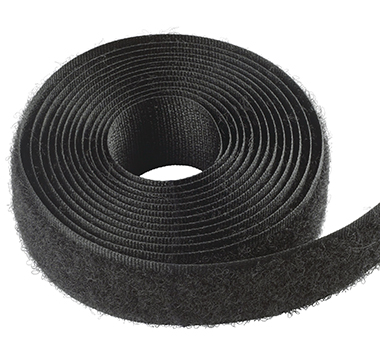
Case Study Converting Experts
Unable to obtain them directly from the manufacturer, a distributor turned to Budnick to supply and convert hook and loop dots.
- Hook and loop dots would be used for promotional displays in a cell phone retailer
- 3/8’’ diameter hook and loop dots were processed after laborious trial and error
- Budnick provided the dots to the customer in pancake rolls as well as spools
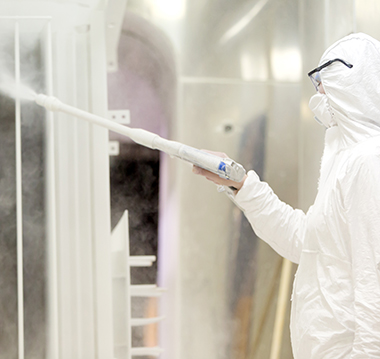
Case Study Process Review
This customer was spending far too much time masking cabinets before wash and baking cycles, having to use different tapes for each step.
- Process review was performed with a trusted tape manufacturer
- Implemented a tape that withstood both the painting and powder coating processes
- Converted products saved the customer valuable production time