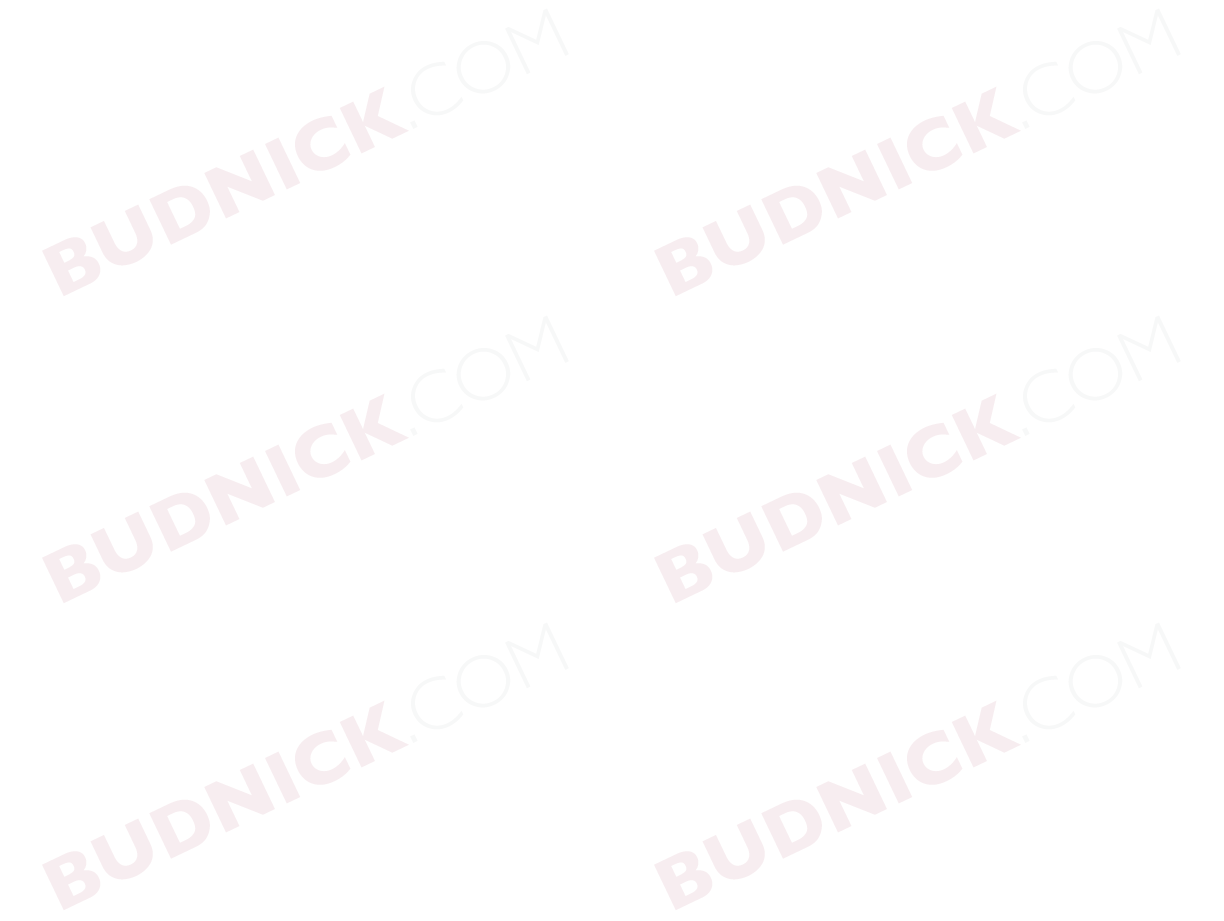
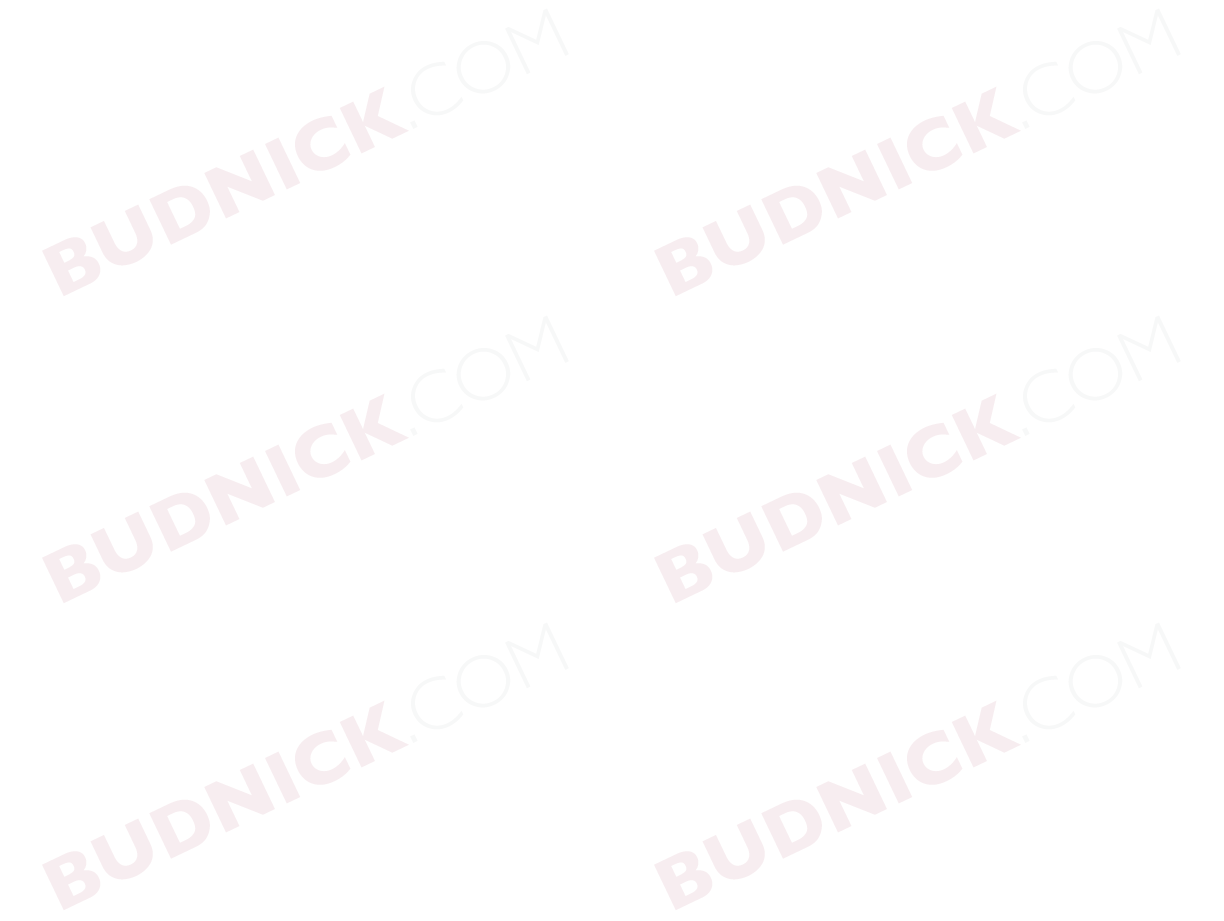
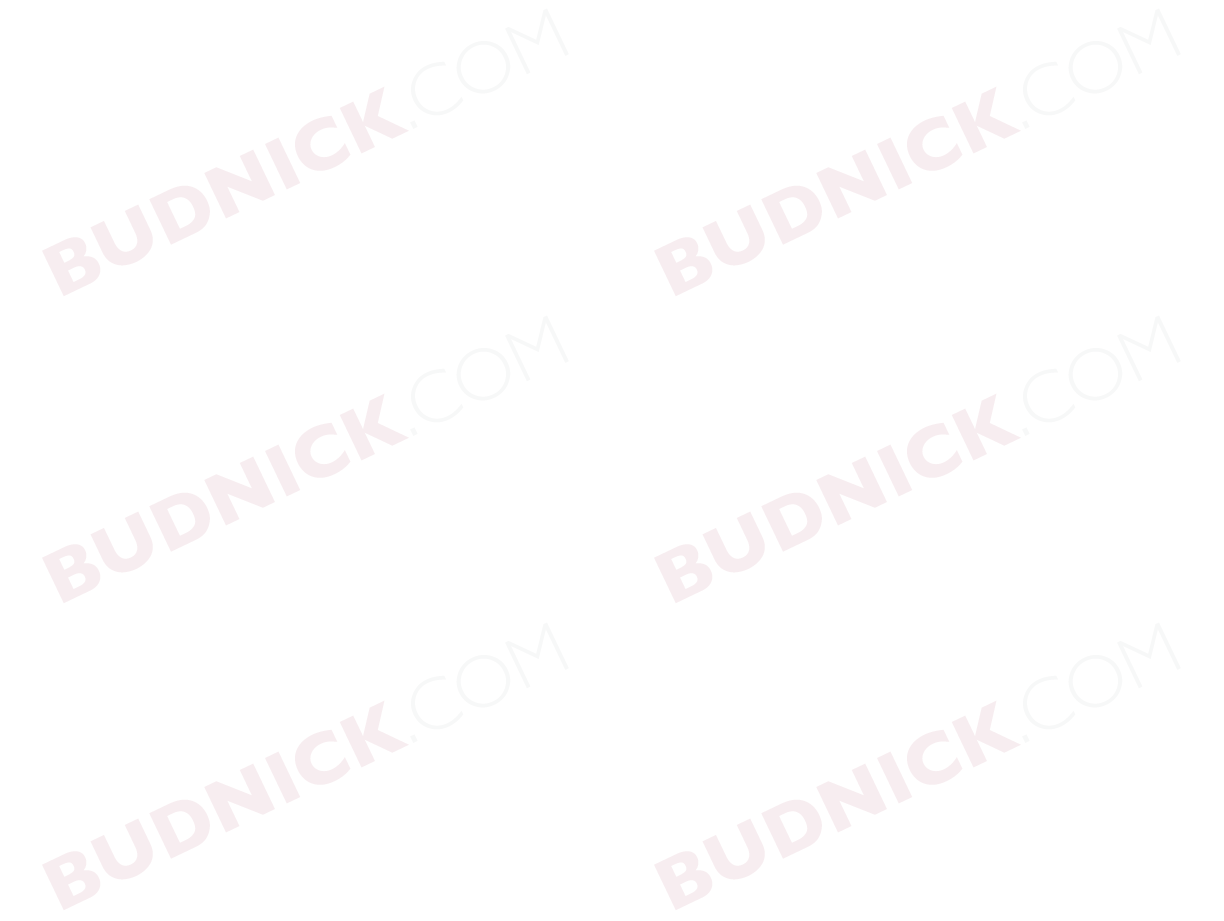
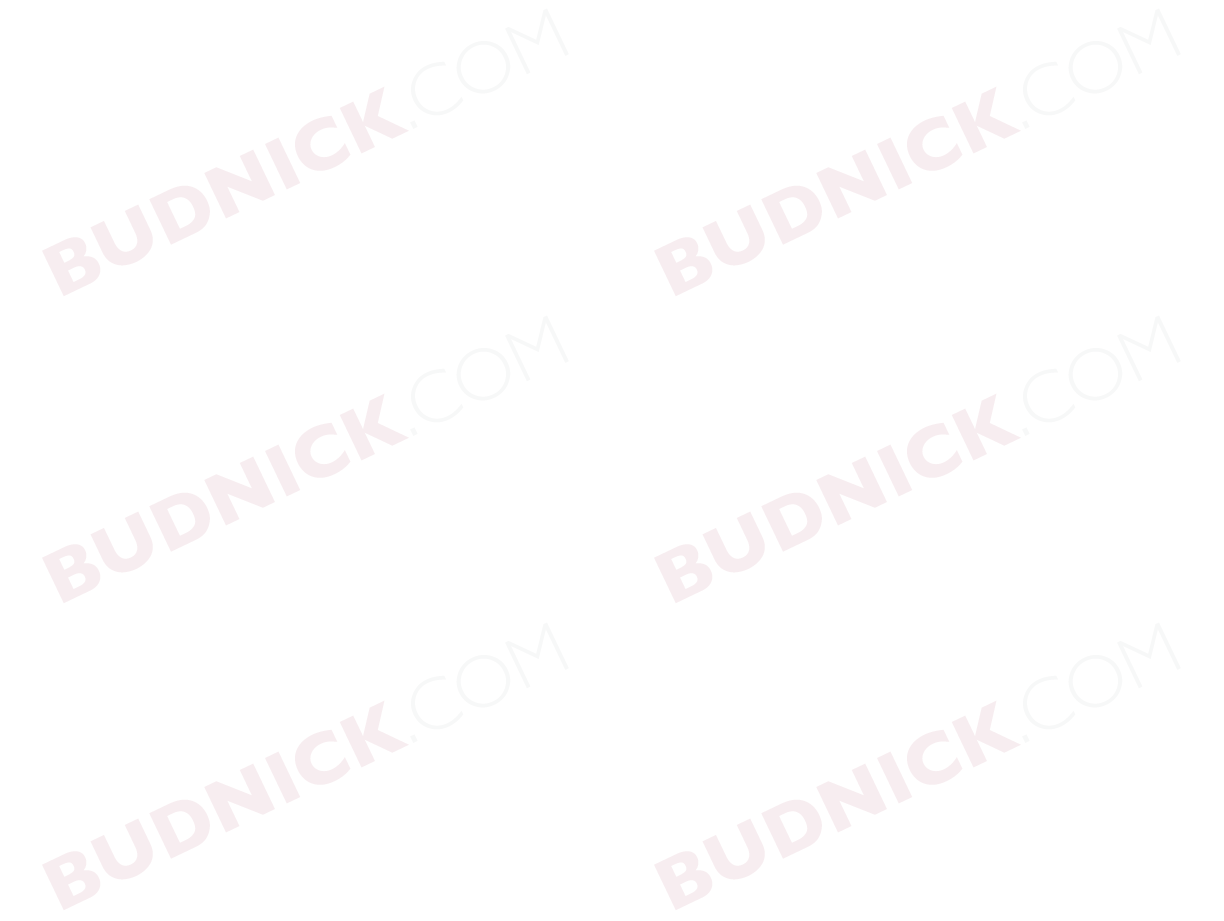
Case Study - Budnick's Process Audit
Customer Need
An interior sign manufacturer was looking for solutions for several application, product, and production enhancements. They needed an aggressive tape to mount and bond various layers of acrylic signage. The customer was looking for an alternative to replace a combination of a liquid adhesive and an expensive high bond tape to mount lightweight foam signage. The customer was also looking for a product to create a gap between two pieces of acrylic signs so a printed piece of paper could be inserted and easily removed. Increased production times were a necessity as well. The customer also wanted to phase out the use of a cutting machine in their facility.
The Budnick Solution
With a variety of needs, the logical solution was to perform an in-depth process audit. This review allowed Budnick to determine solutions to increase efficiencies. Budnick met with the engineering department to educate them on adhesive properties and the difference between acrylics and rubbers, as well as options to increase production times.
Budnick suggested a transparent double-sided tape replace the previously used acrylic tape that had failed to bond the acrylic signs. The recommended tape has a tackified acrylic adhesive which provided a stronger bond and is transparent in color which was necessary for clear displays. A double sided acrylic film proved to have sufficient bonding strength to mount foam signs and replaced the liquid adhesive and high-end bonding tape used in the application. The acrylic adhesive was far less expensive than the previously used silicone.
When it came to finding a solution to create a gap between two acrylic signs, Budnick chose an acrylic foam because of the thickness that it created, allowing a small gap for a paper to fit. It was also decided to add die-cut squares to each corner and to put an extended liner on one side to ease in the application and removal of the poly liner. To increase production efficiencies and eliminate a cutting machine, Budnick created custom die cuts, kiss cut on a liner so the assembler could easily pull and place the product.
Enhanced Productivity
Due to the review of the customer's actual processes and working directly with their team, we were able to see clear areas that could be improved and determine the ideal customized solutions to increase their efficiency significantly.