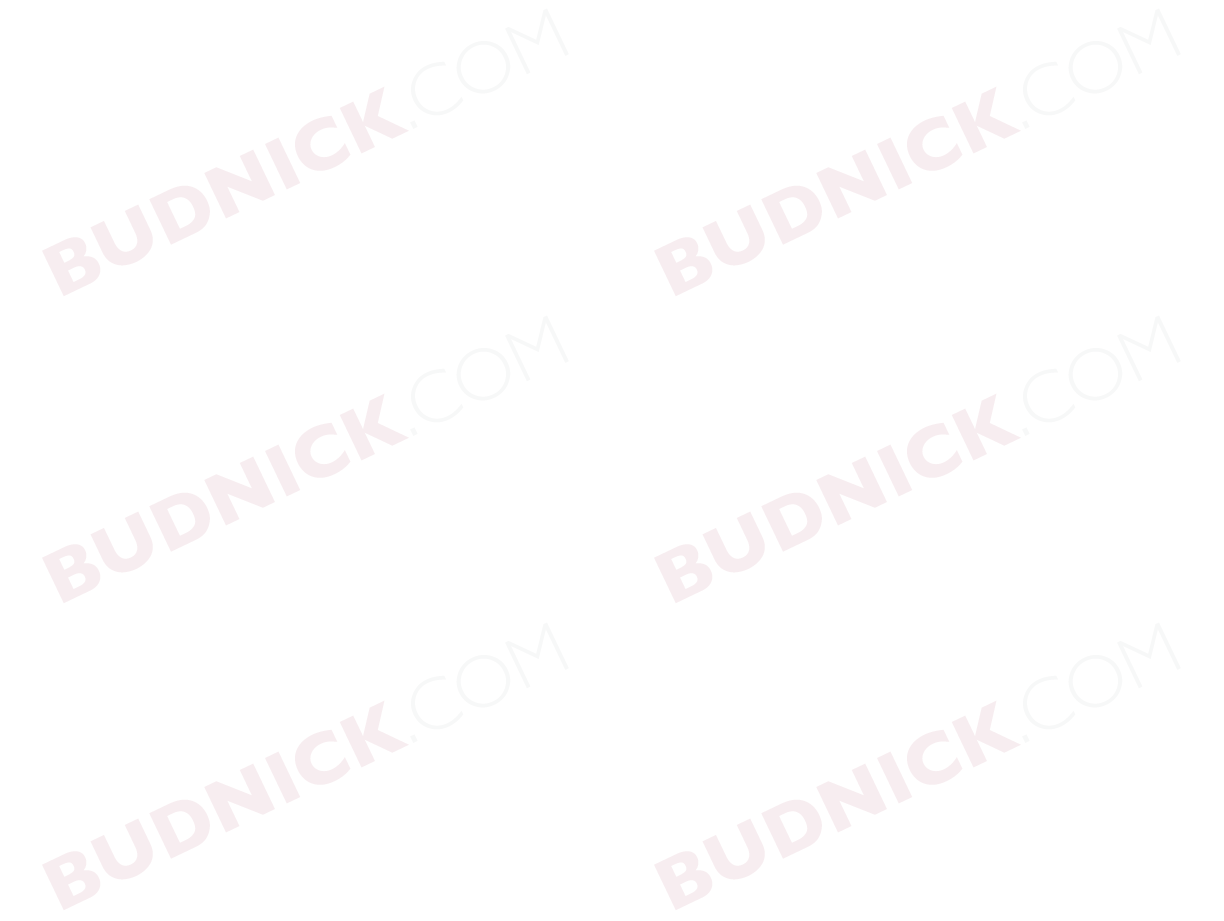
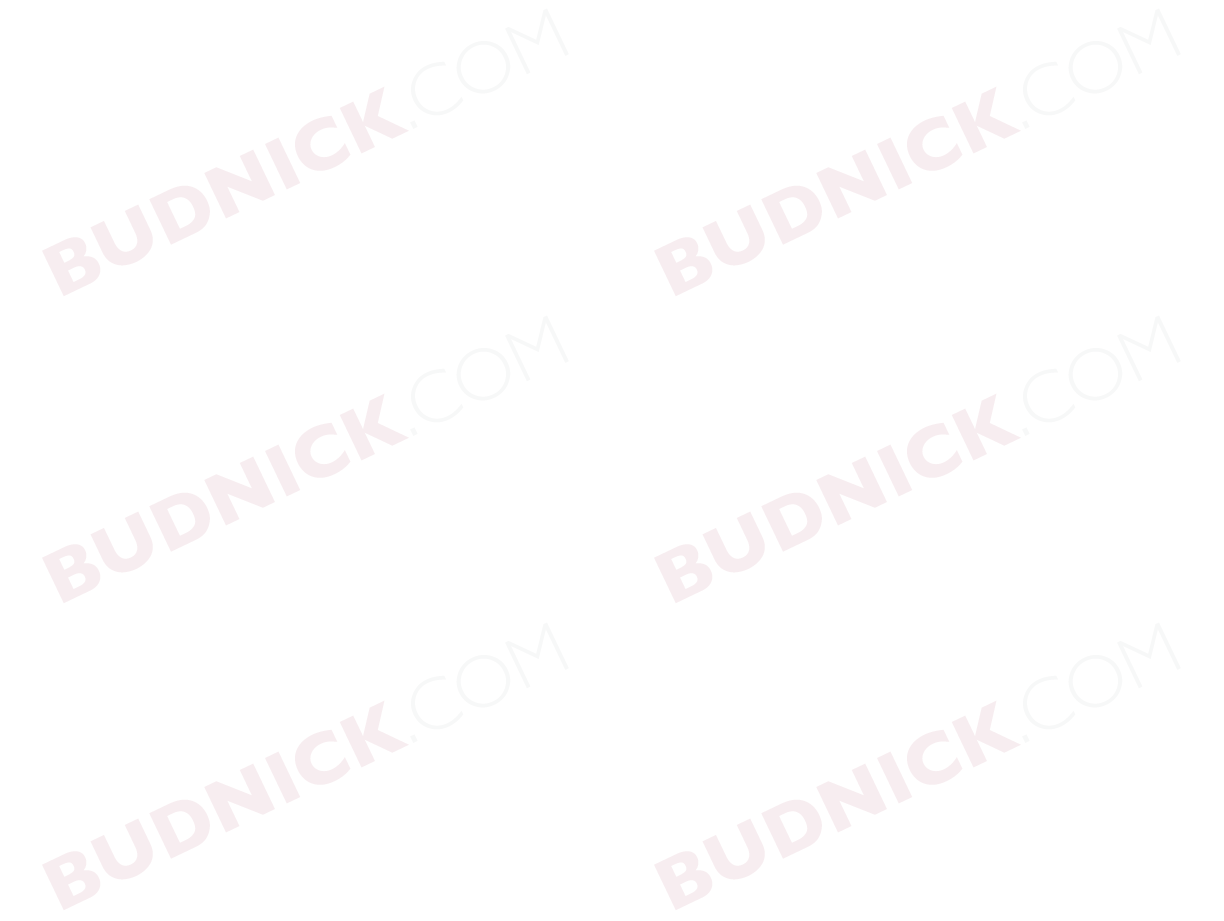
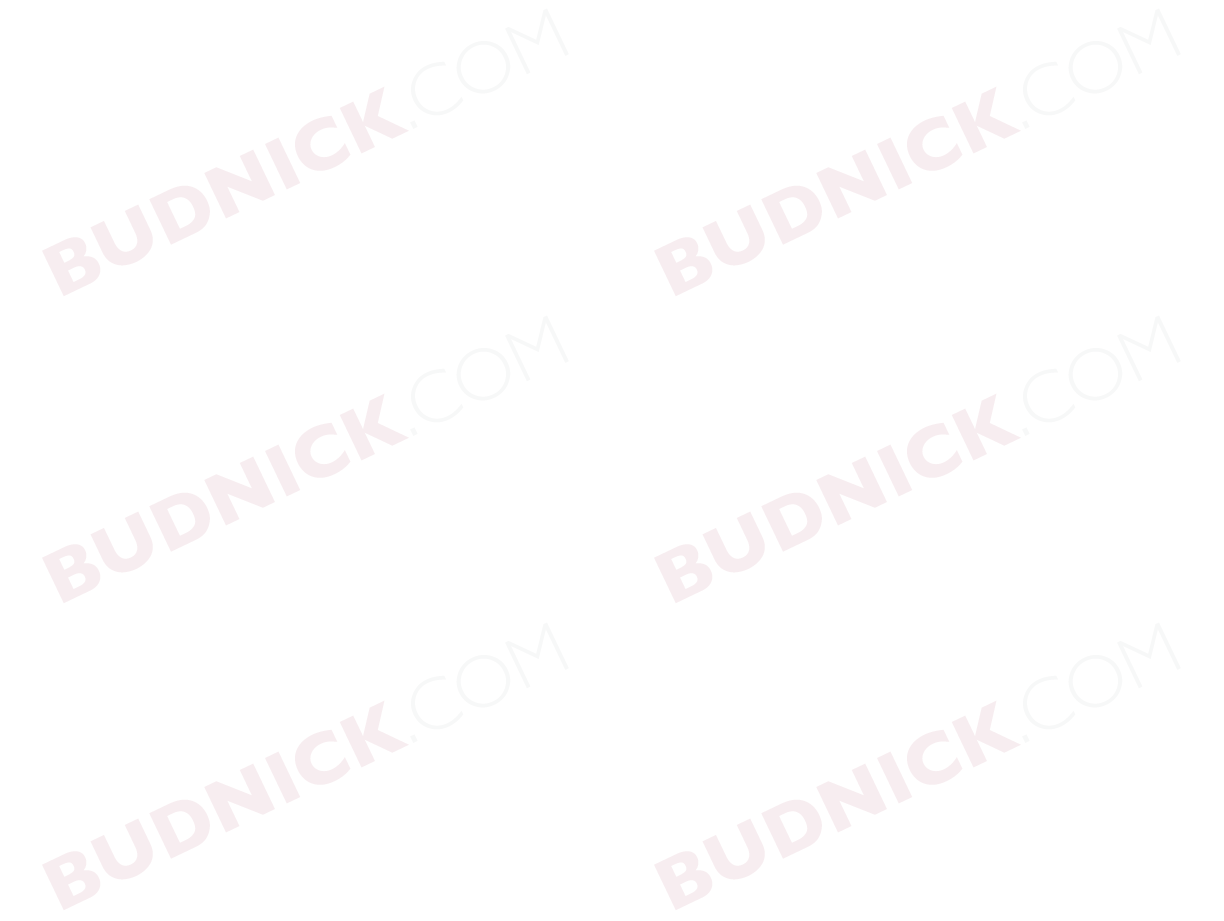
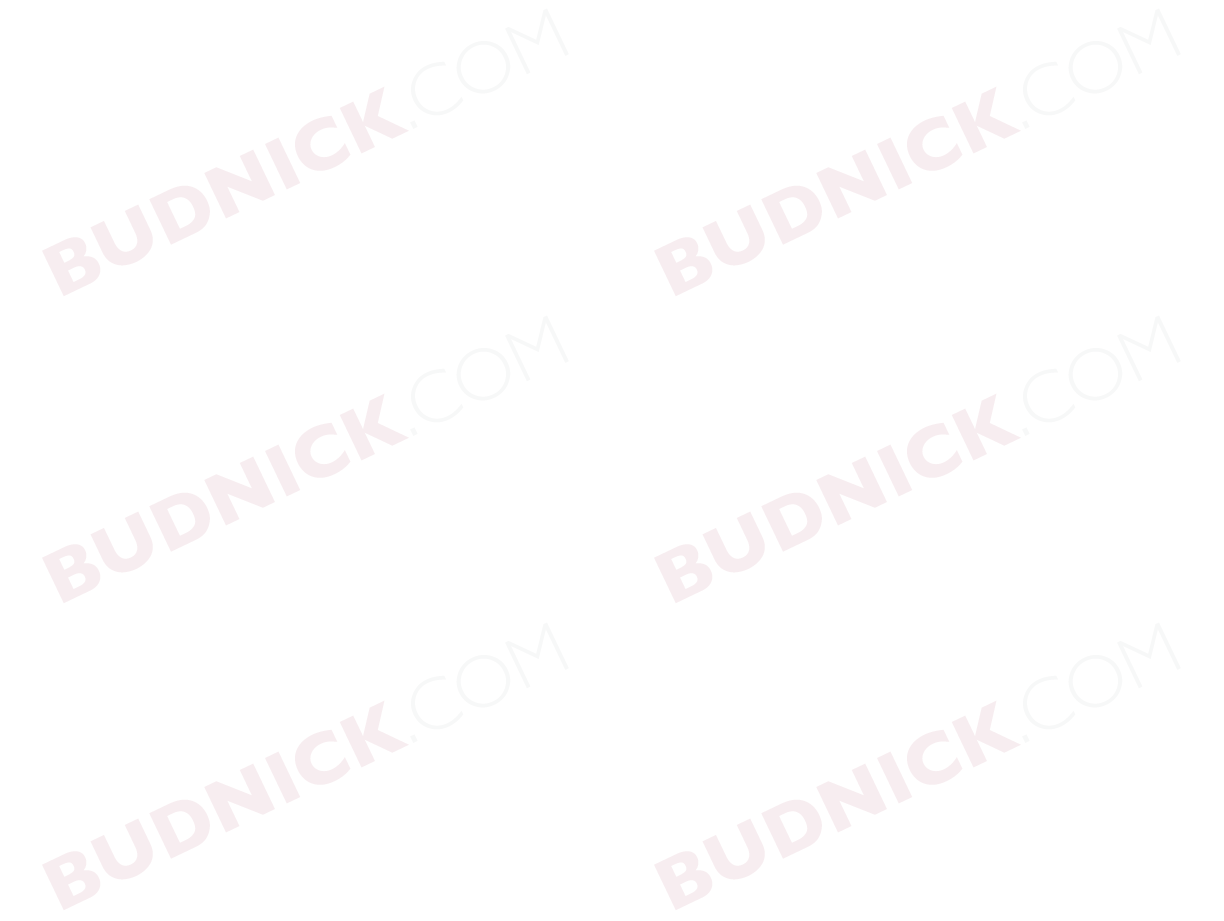
Case Study - Scrap Reduction
Customer Need
A well-known appliance manufacturer wanted to streamline their process when it came to tape usage, decreasing the amount of tape that was being used on each refrigerator unit. The appliance manufacturer’s foam-in-place insulation application was becoming a serious problem as well, with 30% of the doors having to be scrapped. The doors could not be re-worked after having been processed. The customer’s bottom line was taking a major hit.
The Budnick Solution
We converted a product that allowed the foam to expand properly and in the correct amount of time. It is designed to hold foam insulation in and allow more air and gas to escape during foam-in-place injection. To reduce tape usage, we die-cut an arrow so each production worker would apply the same amount.
Serving You
Anytime a customer has to scrap 30% of their product, it is a serious concern. To ensure we indeed did have a solution to solve the customers, problem, we sent two of our tape specialists to the customer’s production plant. We worked directly with production workers, educating them about the adhesive product and the correct way to apply it. In the end, the tape savings were not as large as originally planned; however the savings from the reduced amount of scrapped doors greatly surpassed them. The number dropped from nearly 30% to under 5%, resulting in $400,000 in savings for the customer.